Top 10 Tips to Reduce Inventory Write-Offs
- By Daniel Todd, Nexstar Network Inventory Management Coach
Are your Covid-era inventory decisions coming back to haunt you in the form of write-offs? If this sentence: “The world is out of everything, and my business needs to have significant stock at the shop” sounds familiar, they might be.
And it’s hard to fault inventory decisions made during Covid. It was a crazy time! We didn’t know what was going to happen. Fast-forward to now, however, and lead times and backorders have become more normal. In some cases, excessive inventory levels still exist. Now’s a great time to remember that slow-moving and non-moving inventory is always a poor use of cash flow, but especially so when interest rates are higher than we’ve seen in years.
Don’t panic. There are ways to reduce your write-offs. Here are 10 tips that will make a big impact:
- Complete a usage review of your warehouse and truck inventory to reduce slow-moving and non-moving parts and equipment. Return items to your vendors as needed.
- Think of your inventory in buckets and complete the bucket exercise:
- Bucket 1 – Items that are core truck stock or job materials that can be consumed – these are items the business wants to keep in stock.
- Bucket 2 – Items that can be returned to your vendors that may not be core stock –accepting a restock fee would be OK for these items. In some cases, items might be out of box or scratch-and-dent and be sold at a discount, or a higher commission rate.
- Bucket 3 – Items that need to be scrapped, trashed, or donated to charity. These items may be an asset on the balance sheet, but perhaps they haven’t been sold in years. The rule of thumb is anything that has not be consumed in a year is of “no value” and needs to be written off.
- Get a handle on the digital allocation of parts that have been physically consumed. Here’s one way to approach this. At debrief, dispatch and technicians should connect to review which parts were used from their service vehicles. If there are inaccuracies, some contractors will have dispatch review item by item.
- Secure your warehouse inventory with controlled access.
- Perform full physical warehouse and truck counts at least twice a year. Quarterly is best.
- Perform scheduled monthly or weekly cycle counts of warehouses and trucks. A cycle count is a micro-count – an example of this would be a count of a few bins. Cycle counts are the only way to bridge the gap between full physical counts.
- Get excess materials left over from jobs under control. Here’s how. Add a bin to your vehicles called “Excess Materials.” When the technicians pick up their replenishment, they should drop off the excess left over from jobs.
- Tighten up the return processes in your business. It’s best-practice to make sure returns are completed by the job, not by the department.
- Centralize your purchasing, and limit those in the business authorized to purchase.
- Curious to learn more about these processes? If you’re a Nexstar member, join us for our March 12-14 Inventory Management Workshop in Bloomington, MN. If you are not a member, but curious to learn more about our mission to turn the world’s best tradespeople into the world’s best businesspeople, click here.
Daniel Todd, Nexstar Inventory Management Coach, focuses on improving Nexstar members’ inventory and warehouse systems and processes. He brings 20 years of experience in both supply chain management and operational coaching and support.
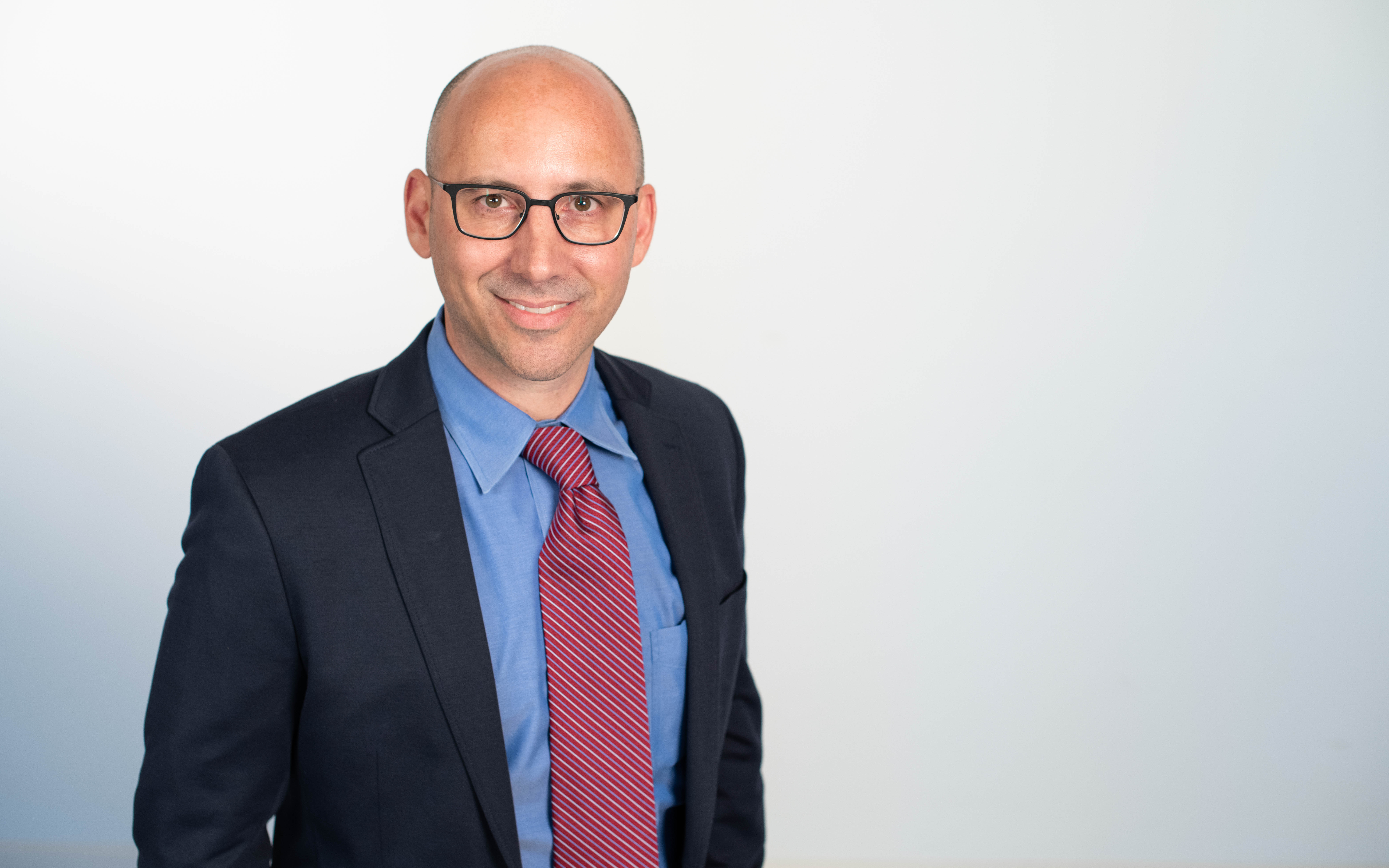